Whether it is the Corona pandemic, the Suez Canal traffic jam, Brexit, changes in purchasing behaviour in the private sector or companies threatened with insolvency - the shortage of raw materials and the resulting long lead times in the international movement of goods are omnipresent. The vulnerability of logistics chains increases disproportionately in the volatility of international economic markets. Currently, missing computer chips are not only causing production losses in the automotive sector, but Covid 19 cases in ports are leading to considerable delays and price increases in logistics. These are just a few prominent examples.
In addition, companies have to deal with new legislative requirements. The Supply Chain Sourcing Obligations Act will come into force from January 2023. It obliges companies to demonstrate compliance with standards on human rights and environmental protection. Companies need to build better capabilities to detect supply chain incidents early and get back into a good position quickly. In combination with other diverse risks and new legal requirements, a multi-level and combined approach to purchasing is necessary.
Stage 1 applies to short-term supply protection through Critical Parts Management. The aim here is to ensure internal production and avoid disruptions to customers. Companies must be enabled to have critical production materials and spare parts at their disposal or to have them delivered in an acceptable time. A contingency plan for critical materials and components must be drawn up and a monitoring system developed in order to be prepared for delivery failures. Stress tests are used to test effectiveness. Ensuring transparency of inventories at production sites, permanently examining possibilities for standardization for products to be procured, quickly qualifying alternative suppliers and communicating closely with customers are among the measures to take countermeasures and secure supplies.
Companies should also use the systematic integration of internal and external stakeholders to implement value analysis approaches. With the help of such value analyses, for example, supply security can be increased - for example, by simplifying product functions. The critical review of product specifications that this could entail also allows alternative materials to be identified. This results in two positive effects: Security of supply is increased through an expanded supplier base, and costs can be reduced through the use of alternative materials.
Value chain alliances with customers, suppliers and other corporate partners open up further opportunities. In logistics, freight ships can be rented jointly or entire production lines can be occupied by suppliers by bundling demand. After analyzing and identifying all critical parts, a Critical Parts Dashboard provides real-time, relevant risk information.
Stage 2 focuses on the medium-term professionalization of supply chain risk management. The seamless management of risks along the supply chain is only firmly anchored in a few companies. A radical rethinking of processes and better forecasting capabilities are needed to respond more effectively to extreme situations. Transparency to the end-to-end supply chain must be established. This requires smooth and cross-functional collaboration between functions and companies along the entire supply chain network. Company and supply chain structures with processes are to be mapped in real time, driven by data, with the help of a so-called "digital twin". In this way, the resilience of the supply chain can be continuously monitored and the scope of the disruption identified, which is related to the product portfolio and network structure.
Prioritize vulnerabilities by impact and likelihood of occurrence
Once the digital twin has been mapped, scenarios can also be developed using a wargaming approach and weak points identified within the upstream and downstream stages of the value chain. In the next step, weak points are prioritized according to probability of occurrence and monetary impact, and measures are derived with the aim of making the supply chain more resilient.
Once the digital twin is established and an intact supply chain risk management system is implemented, laws pose fewer implementation challenges for companies. For example, the data model can be used to reduce a company's carbon footprint by closing inefficient production or distribution sites without negatively impacting service levels. In addition, the early risk classification of suppliers makes it easier to implement new requirements along the entire value chain, for example to comply with the supply chain due diligence law.
In stage 3 the long-term reduction of risks is achieved through complexity management. In principle, multi-perspective approaches should be pursued in order to keep the multitude of different risks under control. Customer needs and product range have to be analyzed and "margin destroyers" have to be identified in order to reduce or better manage complexity in the company. The challenging task of complexity management is to identify the optimal product variety for the service program and to develop ideal solutions for obtaining it - for value stream, business processes and organizational structure. In addition to functioning complexity management, early risk analysis also offers decisive competitive advantages for the product development process.
For small and medium batch sizes, additive manufacturing, also known as 3D printing, offers another perspective to ensure flexibility and availability. This allows decentralized manufacturing centers to be set up and components no longer have to be manufactured centrally and distributed globally. International flows of goods can be reduced in this way, times and routes in transport shortened, costs saved and the CO2 footprint reduced.
Risk management is systemically relevant for maintaining competitiveness
The critical combination of unforeseen and regulatory requirements will make decision-making processes around the supply chain even more complex in the future. The early implementation of a comprehensive supply chain risk management is therefore systemically relevant in order to maintain the competitiveness of companies.
Both authors are members of the management of Kerkhoff Consulting GmbH, which provides consulting services for corporate clients, in particular in the field of purchasing, optimizes procurement and provides support in supply chain management.
Jens Hornstein focuses on direct commodity groups and digitalization in utilities, media or mechanical and plant engineering.
Stephan Weaver focuses on production, restructuring and change management in the automotive and energy industries.
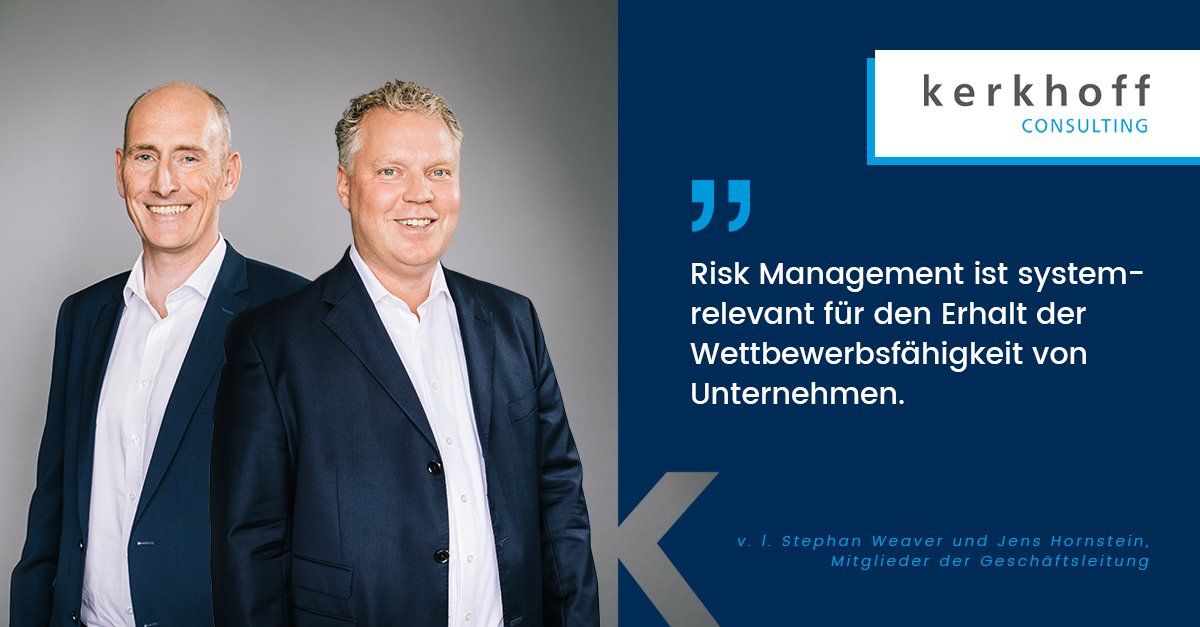